- ベストアンサー
ボーリング作業を効率化する方法はあるか?
- 公差H7の穴をあけるために、ドリルで下穴をあけ、ボーリングバーで1回削り、計測をして、ボーリングバーの調整をして、再度切り込むという方法では機械を止める必要があります。
- この作業を省略し、無人化を行う方法はないか悩んでいます。
- 機械は新日本工機の中型5面加工機を使用し、ワークはt16のSS400のプレートで、穴(貫通)はφ50とφ68のH7です。
- みんなの回答 (12)
- 専門家の回答
質問者が選んだベストアンサー
- ベストアンサー
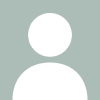
なるほどこの直径だとリーマも無いことはないですがボーリングのほうが早いですね うちでもこの直径のボーリングはよくありますが 初期摩耗を出した後は 結構安定しますよ 1.仕上げボーリングの取りしろを一定にする 2.初期摩耗が済むまでは有人加工にする 3.水溶性クーラントをどっさりかける 加工順 1.下穴 直径で1.0mm残し 2.中仕上げボーリング 直径で0.4mm残し 3.仕上げボーリング 仕上げの条件 チップ:サーメット ノーズR0.4 水溶性クーラント仕様 チョロチョロでなくドッサリかける 切削速度 180m/min前後 送り 0.1~0.15mm/rev 初期摩耗は慣れれば超硬ハンドラッパで擦ってもできますが 加工しながらするのが間違い無いですね
その他の回答 (11)
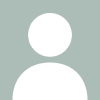
記憶が定かでないのですが 日研工作所のカタログに ”ならし”と称した初期摩耗をとる方法が 載っていました たしか 条件を半分くらいに落として ならして いたと記憶しています 日研に聞いてはどうですか?
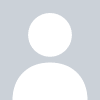
お礼
なるほど。いわゆる1つのノウハウってやつですね。 ありがとうございます。
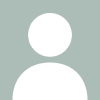
回答(8)ですが、SS400では、出来ないんですか?
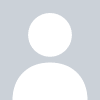
お礼
できないというよりやっていないようです。
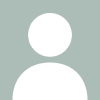
こんばんは アイデアでよろしければ φ68のH7(-0+0.03)なら 剛性のある機械の主軸・アーバー(例LD比2以内)の条件ですが・・・。 とりあえず一度公差の中間(+0.015位)で加工されてるアーバーを 測定します。 測定箇所は、チップの外周先端切れ刃とすぐ近くのアーバー外周部(刃先 とアーバー中芯線上)の段差で、測定器はツールプリセッターを使用し2μ 前後で測ります。 次からはこの段差(2μ以内)でチップの出具合を合わせれば一発で出ると 思います。なお刃物の形状が変わると背分力(寸法に影響する切削抵抗) が変わり、穴径に影響しますので変えないようにして下さい。
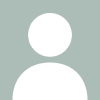
ボーリングより、エンドミルで回したほうが、早いのでは? 機械の精度にもよりますが?
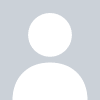
お礼
ありがとうございます。 アルミだとそういうこともやるようですが…。
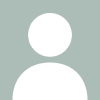
下穴加工>中仕上げボーリング>仕上げボーリングの順にすれば加工寸法は安定します あとはチップの摩耗(寸法変化)を一穴毎に把握して 初期摩耗と安定期と寿命の変化をつかめば良いと思います もちろんですがATCによる微少なゴミへの対策は必要です 直径が大きくてどうしても安定しない場合は仕上げボーリングなど有人加工 の工具ばかりプログラムの最後に集める方法も効果はあると思います
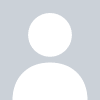
お礼
ご回答ありがとうございます。 加工条件等を追記しました。
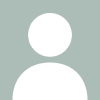
マシニングセンタでしたら、ボーリングバーを何本か用意して 最後の1本で、所定の寸法に仕上げるしかないでしょう?
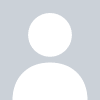
お礼
ご回答ありがとうございます。 加工条件等を追記しました。
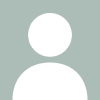
リーマが使用できればそれがベストではないでしょうか? 大径でH7程度の場合、機械の自動測定を使用して合否の判定をしています。浅い穴ですと、エンドミルの円弧切削を使用して補正をマクロで自動修正して再加工しています。。。ただ、この方法はボーリングでは使用できませんね。
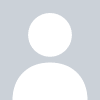
お礼
ご回答ありがとうございます。 加工条件等を追記しました。
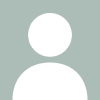
小径ならばリ-マ加工で公差内になると思います。大径の場合はやはり 計測しながらの作業になるのではないでしょうか。 使用する機械によっても違いがありますし、例えば横中ぐりですと ボ-リング主軸を出しての加工になります。ボ-リング主軸自体のたわみも 影響ありますし、熱の問題もあります。 ワ-ク材質、加工径、深さにもよりますが計測しながらの加工がベストに思えますけど。
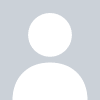
お礼
ご回答ありがとうございます。 加工条件等を追記しました。
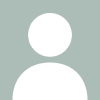
通常、公差は径の大きさによって、同じ記号でも公差自体が違うので 本回答欄に記載してある通り、径と深さを記載してみて下さい^^
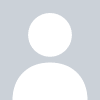
お礼
ご回答ありがとうございます。 加工条件等を追記しました。
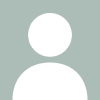
材料、深さが明記してないので、断言は出来ませんが、 私は下穴>リーマ加工でH7公差は加工していましたが、 毎回の寸法確認はしなくても寸法は出ていましたよ。 材料にもよるのでしょうが・・・
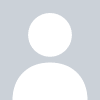
お礼
ご回答ありがとうございます。 加工条件等を追記しました。
- 1
- 2
お礼
ありがとうございます。 何穴ぐらい明ければ初期磨耗がなくなるか、 これはノウハウの世界ですね。