- 締切済み
細穴精度(交差5μ)が安定せず困ってます。
- NC自動旋盤でSUS304 φ5.0の材料でL寸20ミリ穴径φ2.002の貫通穴の加工をしておりますが、規格φ2.002(+0.05/0)に対し、なかなか安定せず全数選別をおこなっており1割ぐらいNGになってしまいます。
- どなたか良い知恵をおかしください。
- ちなみに現在の条件は、下穴φ1.9 仕上げにレアールのリーマ2.005を使用しており回転数1200rpm 送り0.1mm/rev 測定方法は、ピンゲージの通・止めの管理方法です。
- みんなの回答 (5)
- 専門家の回答
みんなの回答
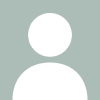
参考までに、当社の加工条件を書きます。 下穴1.94mm加工→HSSリーマー2.005加工 HSSリーマー2.005加工条件、(S380、F18) 加工時間はかかりますが、かなり安定した結果は期待できます。 効率を追求すると、検査の手間が要求されます。 安定した条件で加工すると効率が悪いです。 永遠のテーマですよね。(お互いに頑張りましょう)
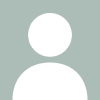
SUS加工の時のポイントが幾つか有りますのでお答えします。 1.加工硬化層が1020ミクロン出ますので下穴を小さくするのは お勧めできません。 2.リーマの芯出しをきっちりする必要がありますので、フローティッ グチャックの使用をお勧めします。 3.切削剤は油性、それも極圧性のものを使用して油膜切れを防止 ください。 面租度と穴径が安定します。 私の経験ではこれで問題は解決するとおもいます。 頑張ってください。
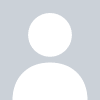
お礼
専門的なご意見有難うございます。 切削油剤は、問題なさそうなので下穴と芯だし作業を注意深く行ってみます。
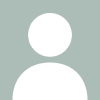
振動切削をトライされては如何ですか?当方も同じような品物をやろうとした時に考えてたのですが、製品化しない事になったためテストできませんでした。URL参照下さい。
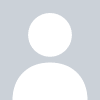
お礼
参考URLありがとうございます。振動切削の効果はすごいですね。 残念ながら現状で経費との問題がありすぐに導入は難しいですが今後の参考として 大変有効な手段を教えていただき有難うございました。
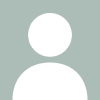
下穴加工をギリギリまで開けて リーマーで仕上げるのが一番の方法ですが SUS304ですと、取りしろが少ないと面粗が出ないのが 一番の欠点だと思います。 方法としては、下穴φ1.9→リーマーφ1.99→リーマーφ2.005 と2回に分けてはどうでしょうか。 かなり安定すると思いますが。
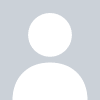
お礼
早速のご回答有難うございます。リーマを2度使うことは考えてもみませんでした.早速チャレンジしてみます。
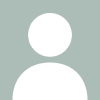
下穴加工をギリギリまで開けて リーマーで仕上げるのが一番の方法ですが SUS304ですと、取りしろが少ないと面粗が出ないのが 一番の欠点だと思います。 方法としては、下穴φ1.9→リーマーφ1.99→
お礼
アドバイス有難うございます。加工効率と検査効率の問題は幣工場でもかなり問題になっております。決められた価格の範囲で加工コスト(サイクルタイム)を割り出すといろいろ弊害がでますよね。トータル的に判断すればよいのでしょうが加工者がわの立場ですと1秒でも・・・と思ってしまいます。 もう一度トータル的にみてチャレンジしてみます。 有難うございました。