- 締切済み
歩留り99.5%を保証するために必要な加工サンプル数
- 歩留りを99.5%を保証するために必要な加工サンプル数について教えてください。
- 1000個を加工して、適合品が995個以上あればいいと言う人もいれば、200個を加工して、199個以上の適合品があればよいという人もいます。
- どちらも感覚的で算出のロジックが分からないため、こちらに質問をさせていただきました。
- みんなの回答 (9)
- 専門家の回答
みんなの回答
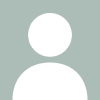
(2)では、数を挙げた例から抜取検査の質問と理解しましたが、 >今、歩留りを99.5%を保証する生産ラインを作ろうとしています。 この歩留りを保証するために必要な加工サンプル数。。。 ライン設計には工程能力 Cpk を出さねばならぬが、そのデータを得るには、加工サンプルを何個作るべきか、との質問なようです。 個数の多い少ないだけては不充分で、日時の経過が必要です。 http://www.sqc-works.com/qc7-03.html X-R( エックスバー アール )管理図の作り方 手順1 管理しようとする項目について、100個ぐらいのデータをとる。 データの取り方は、4~5ぐらいの試料を20~25組とり測定し、データxを求める 日数を経ることによる変動をみるにはこれぐらいが望ましい。工数が多いから試料数は少ない。 逆に自動旋盤の小物加工みたく工数が10秒なら1000個は3時間。数は多いが高々1ロットでグラフにならない。 変動要因として、外気温の変化、刃の切れ味と摩耗、作業者レベルなどあるが、それを含んでない。 下のX管理図 ?~?まで特徴がはっきりした変動があり、表に見方、処置をまとめる。 上のX管理図およびR管理図 特徴は掴めない平穏な推移。 R管理図はバラツキ値なので統計で扱いにくい(試料数が増えると大きくなる) それを標準偏差値に置き換えたのがX-S管理図 http://support.minitab.com/ja-jp/minitab/17/topic-library/quality-tools/control-charts/understanding-variables-control-charts/what-is-an-xbar-s-chart/ 試料は10個 × サンプル数(ロット数)30 試料数とロット数は2例とも同程度。 http://www.kaizen-link.com/statisticals-5.html 長期 Cp/Cpk 工程能力指数を計算するにはデータが100-300あれば正規性の確認も出来るので好ましい ただしこのデータが短期間で採られたデータか長期に渡って得られたデータかで注意が必要 説明の追加は不要と思います。 ロット数を重ねる余裕がなく推測で出さざるを得ないことも多いが、過去の実績があるものなら誤差少ないが、初めての工程や機械ではエイヤー!!
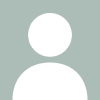
再出です。 オムロンさんだったけ、通称カニフォト(蟹の爪形状しているので)の廉価版は無検査です。 そして、100個の内4~5個は不良品なので、購入時は多く購入してくださいと記していました。 今もあるのかは??ですが。 廉価版なので、その仕様での使い方です。 因みに、通常のセンサは、URLの如く貴殿が記載のよりずっと良いです。
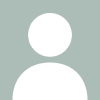
全数検査ではなく、抜取検査を志向なさっているならば、拠りどころとする 基準は、先ずは、JISを利用することが説得力が高いと思います。 JIS検索サイトに規格番号を入力して検索して、 “計数値検査に対する抜取検査手順”JIS Z 9015シリーズの内容を確認なさ ることをお勧めします。 前の回答者さんと共通しますが、歩留りを99.5%をどれほどの信頼度で 保証するかが要点です。100%の信頼度で保障する必要があるとすれば、 抜取検査では対応できずに、全数検査を選択せざるを得ません。
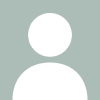
私は質問実績を見てから回答するので 初回の質問者さんには詳細回答はしませんのでご承知おきください。 質問者さんのやりたいことは統計学でいう 「サンプルからの母集団推定」にあたるとおもいます。 >歩留りを99.5%を保証する生産ラインを作ろうとしています。 ○1製品ロット単位の規定と、ロット歩留の信頼度を規定する必要があります。 1ロット歩留の99.5%未満が許されないなら全数検査をするしかありません。 1ロット1000個なら良品を995個詰めて残り5個は未検査品でも不良品でもOKなので最低1000個かロット数の99.5%を満たす良品数が出る加工サンプル数が必要です。仮に検査での合格率50%なら1990個の加工サンプルが必要です。 10ロットに1ロットが歩留り99.5%未満になって良いなど信頼度が下がられるなら、 回答(2)さんの挙げるように抜き取り検査が行えます。 が、必要な有効サンプリング数は ○サンプルの評価係数が複数あるか ○母集団の分布のどこで合否判定をするか などでいろいろと変わってきますので 生産管理工学の専門書籍にあたって頂くか、 あたかもISOに精通されてるかのように振舞われている回答(1)さんに 質問されてみると良いでしょう。
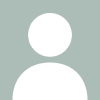
私の実体験です 赴任時 ライン落ち50%以上 早い話半分不良品です 日量要求数 6,000個 40名編成2ライン 投入数6,000個 定時完成数 約3,000個 3,000個を出荷後 残業11:00PM ライン落ち手直し3,000個→これを良品化して翌日分に追加 20年くらい昔の話です これを毎日繰り返し 間に合わなければ 休日出勤でした これって歩留りなんて概念では無いですよね 管理者 作業者 共に 原価意識零 でした 上層部意識は 部品を廃却すると費用が発生するため 極力手直しを要求 していました 実はこれが理想なんでしょうね ただ現場関連の人間には 目先の納品のみが喫緊の現実で効率までは気が回らなかったのだとおもいます 各回答子が述べられているように 不良率を決めて生産するって変だと思いませんか 何個作ろうと 全数良品の意識が 大事だと思います
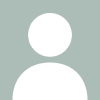
目標は不良”0”ではないでしょうか。 99.5%保証のラインではなく不良”0”です。 といっても不良は発生すると思いますが。 如何でしょうか。
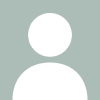
サンプル数 http://www.ceser.hyogo-u.ac.jp/naritas/spss/sample_size/sample_size.htm >>1000個を加工して、適合品が995個以上あればいいと言う人もいれば、 >>200個を加工して、199個以上の適合品があればよいという人もいます。 5 1 ---- = ---- 1000 200
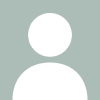
>1000個を加工して、適合品が995個以上あればいい は全数検査です。 検査個数を小さくしたいなら抜取検査。 半導体? 虚な内容を飾り立てる向きには【参考】ルネサスの資料 読みにくいので簡略化したもの http://aql.blog19.fc2.com/blog-entry-15.html まず、検査するロットサイズに従って、 表1からサンプルサイズ文字を探します ⇒ ロットの大きさ501~1200 通常検査水準 ? に仮定 文字 J 次にaql と呼ばれる合格品質水準を決めます。 例えば0.65%であれば、 表2からサンプル文字 の行とaql 0.65 の列が交差した部分を探し、 サンプルサイズ⇒80個 合格判定個数(Ac)⇒1 不合格判定個数(Re)⇒2 なみ検査の一回抜き取り検査であれば、 サンプル数 80個で、不適合品が 1個以内ならロット合格、 2個以上ならロット不合格。 個数を増して厳しい検査を望むなら表2の下方を適用。 例えば200個にするなら不良3個以下で合格/4個以上は不合格 抜取検査は品質管理の教科書に必ず出てます。ネットで拾い読みはいくらでもできるが、理解を深めるには本が望ましいです。 とにかく規格に従うことが大切で、理屈立ては後出しでもいけます。 東芝:半導体製品の信頼性情報 http://toshiba.semicon-storage.com/jp/design-support/reliability/appendix/01/1340336.html ロット個数が同じ例あり 規格はJIS、ISO にもあるが半世紀前からの米軍用規格が有名。 抜取検査は MIL-STD-105 に準拠し AQL 0.65% 通常検査水準? なみ検査の1回抜取方式 で実施します。 こう書けば共通認識が得られ、 表からロット個数に応じた検査個数および合否判定数が決まる。 不良率 AQL 0.65% は表にあるが0.5%は無く、それ厳守なら下の0.4%を適用。計算式あっても面倒なので表の区切りに従う。 品質管理の根本は規定を厳守すること。 検査個数、合否判定個数の線上でランク上げるのがイヤだから、数をチョイ変えて、、、なんてな誤魔化しは絶体ダメ。 >>200個を加工して、199個以上の適合品があればよいという人もいます。 5 1 ---- = ---- 1000 200 抜取検査と似たことになって当然ではあるが、やはり禁じ手。 尚、ロットアウトと判定されての救済方法も定めあります。 >あたかもISOに精通されてるかのように振舞われている回答(1)さんに 質問されてみると良いでしょう 振舞い、装い、お飾り、話逸らすだけなお方なのに・・・キツイ皮肉!!(笑) http://mori.nc-net.or.jp/EokpControl?&tid=309576&event=QE0004 パイプの途中に強引に管用ねじを穿ち盗水するがごとくに我田引水。 否、堤を破り豊穣の稲を呑込み台無しにした小貝川水害の濁流を想起。 乃至はガン細胞が異常増殖の養分を得んがため勝手に血管を巡らす姿に似たり。 既出ルネサス、東芝など半導体会社の資料に詳しいのは理由あってのこと。 (SAMSUNGは英文) 対照的に自動車部品などで不良ゼロを要求されるのも理由あってのことです。
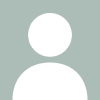
成熟した生産物では、割と低い値ですね。 さて、各工程での付加価値に対しての検査は全て行ない、合格品だけ次工程に送る。 そして、最終検査で、合格品を出荷する。不合格品は廃棄又は修繕をして合格品なら出荷する。 以上の条件で、 ? 最終検査での合格率を歩留りとする(合格品数/最終検査数×100%) 修繕ができて、合格品になる物は、後日合格品数に加えるが、最終検査数に加えない 簡易的な歩留り算出法 ? 各工程での不合格数も歩留り換算する場合、みなし最終製品換算で行なうことが多い その場合に、カウントし難いので、金額換算での歩留りにします (最終合格品数×コスト)/(最終検査までかかった部品や組立て総コスト)×100% 各工程での部品や組立ての設備や人件費、管理費、等々の原価付加し、工程途中での 不合格品も歩留り対象とする 計算が複雑で、資料データ(計算データベース)作成に労力が掛かる歩留り算出法 が、ありますが、ロジック的には如何でしょうか? ISOでも似た管理をしますがね。 ISO等や製品の品質管理上で、自社製品の部品を他社で調達する場合に、調達先工場の 生産工程を確認したり、歩留り状況(技術力の高さや会社信頼度/格付けを測る目的での) の報告を受けたりします。 **年前ですが、SAMSUNGの半導体メモリーで、?に近いデータが原価付きで報告され、 見る人が観れば原価が判るし、どんな原価構成になっているかも判る、お粗末な報告がありました。 そんなことには、ならぬように管理を注意してください。