- 締切済み
※ ChatGPTを利用し、要約された質問です(原文:生産機械の仕様と実際の使用条件)
生産機械の仕様と実際の使用条件
このQ&Aのポイント
- 生産性を考え機械の加工速度の最高値で生産することが一般的ですが、実際には機械仕様の80%程度の速度で使用する方が効果的です。
- 機械設計者の意図は、機械の持ちが良いとされる80%程度の速度で設計されている可能性があります。
- 生産現場での実際の使用条件を考慮し、80%の速度で機械を使用することが推奨されています。
- みんなの回答 (3)
- 専門家の回答
みんなの回答
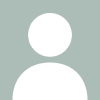
noname#230359
回答No.3
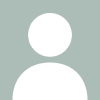
noname#230359
回答No.2
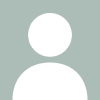
noname#230359
回答No.1
お礼
なるほど、最適なコストパフォーマンスを考えた上で生産条件を決定するのですね。 その中で設備改善を繰返しならがパフォーマンスのレベルを上げて行きたいです。