- 締切済み
キー溝加工(汎用フライス)
エンドミル径方向一発でキー溝加工を行なっています。 材質 SUS304 工具 ハイスエンドミル 加工方法 軸方向に1mmづつ切り込みを繰り返しております。 そこで大体Φ8~Φ14が多いのですが。 軸方向 1っ発で加工出来ないものなのでしょうか? 例えば、送りを落とす、工具再選択、工具をの交換周期を上げる・・・等 何か良いアドバイス、実際この様な加工されている方の声をお聞かせ願います。 品質最優先です。 素人の為、なぜこのやり方をするのかがいつも疑問ですよろしくお願いします。
- みんなの回答 (3)
- 専門家の回答
みんなの回答
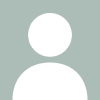
昔、ポンプのキーミゾを加工していました。 SUS304の場合、刃幅いっぱいの加工に成るため、刃持ちや加工面のむしれの発生などから、1発加工は止めた方が良いです。特に超硬はエンドミルの側面が減りやすいので、仕上げ以外使えません。 高品質で効率よく加工をするのなら、2枚刃でコーティングの粉末ハイスを母材としたエンドミルで下加工をしてから、(ハイスの)コーティングのキーミゾエンドミルにコーナーを付けて、送りをあげて仕上げた方が良いです。
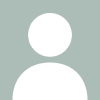
>品質最優先です。 軸方向の切り込みを多くするほど溝がアップカット側に傾くので、 慎重に進めたほうが良いと思いますよ。
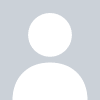
お礼
回答ありがとうございます。 やはりそうですか、身長に進めたいと思います。
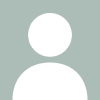
汎用フライスの剛性,主軸の振れ精度などが判りませんが、 1mmずつの切込みは小さすぎるような感がいたします。 特にSUS304は加工硬化しやすい材料なので、エンドミル刃先 のダメージも相当なものと思われます。 どの位の図面指示かにもよりますが、3~4mmぐらい切り込んで みては如何でしょう。 ちょっと認識不足でした。 ミスミさんのキー溝加工用超硬エンドミル http://jp.misumi-ec.com/ec/ItemDetail/10600003650.html において推奨切削条件をみると、切込み深さは0.2D以下と 記載されていました。 キー溝に必要な加工精度を得るには、超硬エンドミルでさえ 大きな切込みはご法度の様です。 ステンレスですし、先ずは切込みを倍の2mmでお試しください。 なお、溝加工ですので、2枚刃のキー溝加工用エンドミルを 使用していれば、アップ/ダウンに関係なく面粗さは送り速度 に依存します。
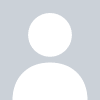
補足
素早い回答ありがとうございます。 機械剛性に関しては表現が難しいのですが 振れに関しては、計測してみます いづれにしても切り込みが大きい程振れの影響は少なくなると思います。 図面支持に関しては、市販のキー材が叩いて入れば良いみたいです 過去に面粗さ?により1mmづつになった経緯があるみたいですが おっしゃる通り刃先がすぐに痛む事も考慮すると やはり3~4mmにして、加工後、溝の入り方で工具交換の判断をした方が 良さそうですね。 ※面粗さについてアップカット、ダウンカットが混在する以上 考えから除外しても良いですよね?
お礼
回答ありがとうございます コーティングに対処して加工時間短縮につなげたいと思います。