- ベストアンサー
φ18キリ穴を面粗いくきれいに早くあけたい方法
- 横型マシニング(2パレ式)において、深さ30ぐらいのφ18キリ穴を面粗いくきれいに早くあける方法を教えてください。
- 現在はφ7.0のドリルで下穴をあけた後にφ18.0の穴をあけているが、面粗が悪いとクレームがあり、面粗いくキリ穴をあけるために下穴をあけている。
- 下穴なしで一気に加工を行う方法や、情報・事例など、どんな情報でも教えてください。
- みんなの回答 (5)
- 専門家の回答
質問者が選んだベストアンサー
- ベストアンサー
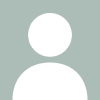
ドリル加工というのは、発生したキリコが内面を削ってしまうので、 基本的にはあんまりきれいにはあかないものです. 下穴があいていた方が、二本目のドリルのキリコの幅が抑えられますので、 表面はかなりきれいになります. また、キリ先にニックを入れておくと理論上は個々のキリコの幅が狭くなりますので、 同じ様に一発で入れたとしてもキリコによる肌荒れを幾らか防げるかも知れません. キリ穴にリーマやタップなど後加工が無いのであれば、超硬ドリルの方が早くかつきれいにあく可能性があります. 超硬ドリルは刃先がわずかにホーニングされているためハイスよりもキレが悪く、 軽く表面をバニシングするような事になりますので、この加工硬化により キリコによる再切削がハイスドリルよりもわずかに置き難くなるハズです. 四角やおむすび形六角のチップを使うスローアウェイドリルは、 実質的に一枚刃のため送りが上がりませんが、 ソリッド風の刃先より穴の表面が加工硬化するハズですから、 その意味ではよりきれいに上がる可能性も無くは無いでしょう. 最近ではワイパー刃の製品も用意されています. 現状、どんなドリルをお使いなので何ともいえませんが、 なお、私が先日試したナチのAG-ESというコーティングハイスドリルが、 溶融ハイスドリルとしては格段に磨耗が少なかったですので そこそこ切削速度を上げても同じくらいの刃持ちが期待できそうですね. 粉末ハイスほどの神経質さ(折れ易さ)は無さそうです. 切削速度が上がれば、回転あたりの送りを同じとしてもテーブル送りを上げられ、サイクルタイムが短くなります. また、私が今まで使った中では、三菱(旧コベルコ)のVA-PDS/PDMは、粉末ハイスのせいか、 やたらと折れる印象があります. それよりは溶融ハイスではありますがOSGのEXゴールドの方が突発的な折損が少なく安心して使え、内面もそこそこきれいに上がります. (下穴があいていると快削鋼ならピカピカになります.) OSGのドリルでもVPゴールドの方は粉末ハイスになりますので、若干神経質さが出て来るハズです.
その他の回答 (4)
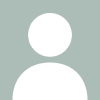
どの程度の綺麗さが要求されているのかですが、 スローアウェイチップでは、サンドビックのスーパーUドリルでワイパーチップにすれば、一番信頼できて面粗度もよい気がします。 加工速度も速いです。 ただし、高速回転によって加工タイムを短縮するので、 油性の場合、危ないかもしれません。 (弊社は水溶性のセンタースルーにて) 当然、センター、下穴なしで一発でφ18で加工できます。
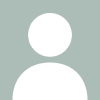
SS,SUSの加工なので、EXです。 カタログ値で、クランプがよければ+0.1以内には納まります。
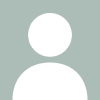
三菱の VA-PDMφ8.5(下穴) 12(下穴) 18 の3本加工 G81で加工する。 ドリルの加工時間を短くして 回数を増やす。 センタ-ドリル不要 クランプがしっかりしているのなら 1発で加工可能(センタ-ドリル不要) スピンドルスル-があるのであれば、 油穴突きドリルもアリです。 osgの油穴突きドリルを主流に使用しています。 当然下穴なしの1発加工が出来ます。
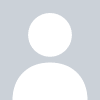
補足
回答ありがとうございます。 まさか3本での加工とは意外でした、、 現在の加工は機械が古くツールチェンジが悲しいぐらいい遅いのです。 一応φ18穴以外にも穴あけしているのでセンター加工は絶対的なんです、、 ただ、違う機械でも似たような加工をしているのでトライはしてみます!!
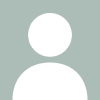
SS400ですが、OSGのゴールドドリルは、下穴なしできれいにあきます。 でもクランプが悪いのでは、カタログ推薦値での加工は無理ですね。切削条件(送り、周速)を、下げると寸法精度、仕上がりは、極端に悪くなります。
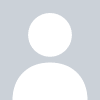
補足
早速の回答ありがとうございます。 カタログで調べたところ、どっち!?的な状況になったのですが、、 VPゴールド・EXゴールドこのどちらかでしょうか?
お礼
回答ありがとうございます。 スローアウェイ式のドリルはうちの機械が内部給油式にしてないので、抵抗・発熱を考えると厳しいかもしれませんね、、、水溶性の機械だったらね~と言われてしまいましたし、、、、 いろいろ調べていてナチAG-ESも候補にあがっていました。 いきなり使用するのは心配でしたが、使用経験上のお話いただけて大変参考になりました。 早速上司に話を持って行きたいと思います。