- ベストアンサー
溶接箇所の塗膜はがれの対処法
- 溶接箇所の塗膜剥離が発生しています。溶接による油焼けが原因だと判断されています。
- リン酸鉄皮膜処理後に粉体塗装を施していますが、最近は塗膜の剥離が多くなっています。
- 溶接部のスケールや残留油の除去方法を探しています。何か良い方法はありますか?
- みんなの回答 (2)
- 専門家の回答
質問者が選んだベストアンサー
- ベストアンサー
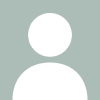
当り前の事で恐縮ですが、残留油は原因を元から断つしか合理的な方法はないようです。昔はトリクレンでデッピング洗浄したり、オガクズの中で回転洗浄したりもしていました。用途、製品形状、数量などわかりませんが、当社の場合、従来の鋼材の防錆用油はメーカーに話して極力減少させ、タイムリーに入荷させるなどの工夫をして標準の脱脂工程で取れる程度のものにしています。事前の処理と事後の処理のコスト比較、です。 スケールについてはスチール家具の業界のケースですが、基本的に見える部分は溶接を避け、他の締結方法を選択します。例えばボルトナット、圧入、カシメなど。強度的にどうしても溶接が必要な部分は、プラスチックなどのカバーをデザインして、溶接のビードや塗装の難易度をまさにカバーして避けています。トータルで見栄え良く、如何にコストを下げるか、という業界ですが。 スケールはやはりどこかの工程の空きで半自動研磨などで工数を増やさず処理する方法かと思います。
その他の回答 (1)
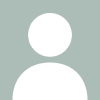
ご参考にならないと思いますが。 小生も溶接部位の塗膜剥離は経験しています。ただ抵抗溶接などの酸化皮膜ではよくありますが、炭酸ガスシールド溶接などではあまり問題になりませんが。溶接部位は静電塗装が微妙に乗らず、塗膜の安定には苦労しています。 皮膜処理前の洗浄、皮膜後の水洗がしっかりしていればあまり起きないと思います。抵抗溶接などの酸化膜を完全に取るために研磨や薬品処理もしましたが、結局は溶接部位を如何に少なくするか、かと思います。板金の接合では突起を出して大電流を短時間にという方法なら焼けがほとんどなく、塗装では問題ない、という経験もあります。 残留油はよく理解出来ません。
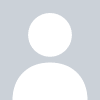
補足
早速の回答ありがとうございます。 問題になっている溶接は、TIG溶接で一箇所に集中 して溶接をしています。確かに大電流で短時間で あれば問題ないのですが、TIG溶接のため時間が かかっています。 残留油は、溶接に時間がかかるため、油焼けを お越し溶接部周辺に焼きついてしまいます。 その油が前処理で落ちないのです。 今は、前処理前にシンナーで除去している 状態です。
お礼
ayanoさんありがとうございます。 実は、我々もスチール家具業界の者です。 何とか低コストで処理できる方法をと思い投稿したのですが、やはりayanoさんの言われる通りだと思います。再度、仕様から見直してみます。