- 締切済み
端子締め忘れヒューマンエラー防止の方法
- 設備保全を進める中で、端子の締め込み不良や差し込み不良などのヒューマンエラーによる故障対策が求められています。
- 端子の締め忘れ防止や差し込み不足の対策について、アドバイスや事例があれば教えてください。
- ヒューマンエラーによる端子関連の故障を防ぐためには、正しい取り扱い方法や点検・管理の徹底が重要です。
- みんなの回答 (7)
- 専門家の回答
みんなの回答
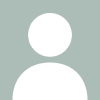
あんまり役に立たないかもしれませんが意識改革が一番の解決に繋がると思います。 私が以前働いていた会社は 交通関係の会社で一つのミスが数千万人に影響しました。(被害は数十億円) 何か作業をするときは監視者を1人決め その人は図面と赤ペンだけを常に持たせて配線を外したら図面の該当箇所にマークを入れるという仕事ですね。 実作業をしている人も常に監視者がマークを入れたかは気にしていました。 外し、戻しの赤マークを監視者が入れ作業完了前に 全員でそのマークと現物を確認して直筆でサインしていました。 そうすることで責任というものを明確化していました。 その会社では作業に関してのヒューマンエラーはありませんでした。 (交通事故などはありましたが…) 作業でのヒューマンエラー=左遷という会社でしたので。。。 一つのミスがいくら(のお金)になり それが自分達の給料に直結していることを強く意識の中に組み込むかが ヒューマンエラーの防止に一番繋がると思います。
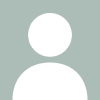
端子台については先にも提案しましたがフェニックスコンタクト製の圧接式(QTシリーズ)ならばレバーを下げる事で配線される物である事からレバーの状態で確認できると思います。(但し、個人的には構造面で経年による接触不良が懸念される為、使用までは考えていません。)一度、カタログ等で確認してみては如何でしょうか。電ドルについては盤屋さんでは有りませんので詳しい情報は持っていません。
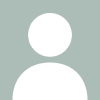
この場合の保全作業とは センサー故障で交換したとか 電磁開閉器の接点が寿命になったので交換したとか モータが焼損したので交換したとか そんなのですよね ベルトコンベアでの流れ作業では無いのですから 通常、よく言われるヒューマンエラー対策は使えませんね 使用するビスを前もって数えて置くとか 使用る工具のみを作業台に置いて、今使わない工具はすぐに返すとか 増し締めマーキングも多くの場合、製造メーカでしてるので 再度マーキングしても 真っ黒になるだけ 単純に端子台での増し締め忘れ防止なら 所謂、ダブルチェック 作業者では無い検査者が増し締めする それと、電線を手で引っ張って更に左右に振る 閉め忘れならそれで分かります 手で引っ張ったくらいで切れるようなら圧着不良 センサとか0.2sqの線は圧着不良ですぐ切れる 0.2sqでも正常に圧着出来てる端子を引きちぎるには相当の力が要ります
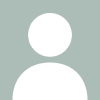
カテゴリーが保全なので、 1本毎に、ネジ締付け後マーキングをする が良いと考えます。 駅等の端子は、安全上見る事はできませんが、 鉄の構造物のボルト止めは、ペンキでマーキングしています。 締め付け後のマーキングと、その直後のチェックを兼ねた増し締め マーキングを色を変えて行う場合もあります。 端子の差し込み不足は、皮剝きの長さ管理と、端子タイプ毎の セット形状(長さ)管理をして、OKなら(色を変えての) マーキング管理をしたら如何でしょうか?
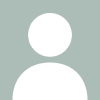
はじめまして ?一般的ですが、ネジの締め付け後にマーキングをする。 多分、この程度のことはすでにお考えになっていることだと思いますので ?電動ドライバーの使用が可能な部分については、スクリュカウンタの 使用を検討されてはいかがでしょうか
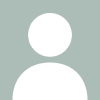
100%の対策にはなりませんが、 ジャンプアップ型の端子台やフェニックスコンタクト製のダイレクトイン式、圧接式端子台等の採用も一つの選択と思います。
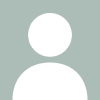
ヒューマンエラーの対策は非常に難しいですよね。 例えば、外した配線などにタグをつけては… 締込みを行なった後、差込不良・締込み不良を確認した後、タグを取る様にすれば、いきなりゼロにならないかもしれませんが、徐々に意識が高まるのではないでしょうか。
補足
アドバイスありがとうございます。 端子へのマーキング等は行っているのですが、 なかなか作業員全員への周知ができず、 また、故障調査時の作業員が復旧することに慌てて 端子の締め忘れによる故障が時々発生しているのが現状です。 そこで、ハード的に端子台をビス式ではなく、 ダイレクトイン式の端子へ変更する案が作業員の中から出ています。 しかしながら、工場内への水平展開を考えると ビス式端子台をダイレクトイン式端子台へ変更するには 費用、場所、労力等を考えると 現実的ではありません。 そこでたけさんからアドバイスを頂きました ジャンプアップ型端子台や フェニックスコンタクト製ダイレクトイン式の他に 何か現実的にハード面でヒューマンエラーを防止できるのもは ありますでしょうか? 今考えているのは、ダイレクトイン式に変更するか (但し小型リレーのソケットはダイレクトイン方式の物を 選定できたのですが、マグネットスイッチ等の補助接点が ダイレクトイン方式の物が選定できていません。) 工具を電動ドライバーに変更し、 締め込みが終わるとクラッチで回転が滑るものがないか 現在選定中です。 電動ドライバー等も含め、 何か良い物があれば教えて下さい。