- 締切済み
加工時間を短縮!skd11の加工方法と加工ツールについて
- skd11の加工時間を短縮するために、G83からG73に切り替える方法を探しています。皆様はどのように73と83を切り分けていますか?工具直径の何倍の板厚なら83を使うのか、ルールを教えてください。
- また、現在の形状加工にはフラットエンドの二枚刃を使用していますが、普段はフラットエンドは仕上げ加工にしか使わず、ラフィングエンドという超硬のツールで加工しているそうです。加工時間を短縮するためにはどのような工夫がありますか?アドバイスをお願いします。
- みんなの回答 (4)
- 専門家の回答
みんなの回答
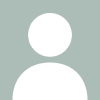
マクロが自分で組めるのなら、 たとえばG73+G83のドリルサイクルとか作れるので、 加工時間短縮には有効でした。 普段、G83で穴を開けている所も途中まではG73で加工して、 穴が深くなってきたらG83に切り替えて加工。 切り替える所は正直、良いアドバイスが出来ません。 機械や工具、品物の形状等、一概には言えないので 色々と試すしか無いと思います。
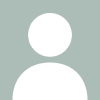
お気に入りだった工具 http://www.amazon.co.jp/%E4%B8%89%E8%8F%B1%E3%83%9E%E3%83%86%E3%83%AA%E3%82%A2%E3%83%AB-MITSUBISHI-%E3%83%95%E3%82%A1%E3%82%A4%E3%83%A4%E3%83%BC%E3%83%9F%E3%83%AB-BRP4NR253S25/dp/B00VHO3SKC 過去形なのは ましにんがーだったころの努めていた会社はつぶれてしまったから 自己カミによるチッピングはまずしません スローアウェーイみたいに心臓に悪い音は出ません 静かです ドリルは 30mm以上は G83 ドリル径5mm以下も G83 それ以外は G73 でした 平気でG81を使ってる人もいるが 怖くて勇気がありません >>30mm以上は 板厚です ドリル径で1.5Dで切り替える人も多いですが 大きいほうは φ12以上は下穴あけからの G73 φ15以上はエンドミルでの拡大 下穴あり φ22以上はスローアウェーイにての拡大 下穴あり
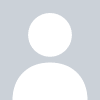
補足
ありがとうございます。30ミリと言うのは直径ですね? 15φ以降はエンドミルでの拡大というのは エンドミルで繰り広げてその径にしていると 言う事ですか?ドリルは下穴だけで
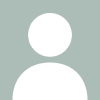
回答するための手材料が少なすぎます SKD11は焼き入れ前ですか?焼き入れ後ですか? ドリルはハイスですか?超硬ですか?穴深さは?給油方法は? マシニングセンタの主軸テーパサイズは?最高回転速度は?年式は? 穴加工は径の2-3倍までの深さであれば外部給油でもノンステップ 加工が可能です それ以上の深穴でも内部給油であれば同様にノンステップが常識 になりました 外部給油でも、ドリルの先端形状や溝の技術進化により、昔ほど 頻繁にステップを刻まなくても、深穴加工が可能になっています 今一度、使用されるドリルの見直しをされることをお勧めします 先ずは、出入りの工具屋さんもしくはよく使われるメーカのフリー ダイヤルで相談してみては如何でしょう エンドミルの荒加工であれば、最近は刃先交換式タイプを用いるのが 主流です φ20×3枚刃ぐらいが使えれば、切削速度や送り速度アップによる加工 能率向上が可能です もちろん、それよりも小さい工具径が必要な場合は、超硬ラフィング エンドミルの使用も有効です さらに溝やポケットは3枚刃、側面は4枚刃の超硬エンドミルを用いれ ば、刃数が増える分だけ送りが稼げて、加工時間短縮につながります 刃先チッピングを防ぐため、荒加工はピン角ではなくラジアスエンド ミルを使用することも一案です 仕上げ加工も同様に4枚刃を用いれば、加工時間が短縮できます 古いマシニングセンタでなければ、送り速度をUPしても、加工精度への 影響はそれほど大きくないと思われます >>あら加工はラジアスエンドとラフィングエンドはラフィングエンドの方 >>がよいですか? これは好みです BT50のマシニングセンタであればラフィングでバリバリするのにも適して いますが、そうなると刃先交換式工具の方がより重切削に向いています 一方、ラジアスエンドミルは、先に仕上げ加工に使用して、摩耗したら荒 加工に使いまわすこともできます ラフィングエンドミルは切削抵抗が低いので深切込みの加工が 可能です しかしチッピングしやすいので、送り速度はあまり早くできません 一方でラジアスエンドミルは、どちらかと言えば切込みを小さく して送りを早く加工して能率を稼ぎます 乱暴な表現をすれば、トラックとスポーツカーでどちらが仕事に適して いるか?と問われれば、前者はたくさんの荷物を運ぶことができ、後者 は高速でぶっ飛ばすことができ、仕事の内容が異なる訳です >>プレス金型の加工ではピン角のフラットエンドでないとまずい >>部分は何かありますか これは、ケースバイケースで、図面によってそちらで判断して下さい 垂直にそそり立つ壁の底部がピン角に指定してあれば、ピン角フラッド エンドミルが必要となりますが、Rをつけたり逃がしを付けたりする 設計が多いと思います 加工の細かい内容については、100回文章で説明するよりも1度削って みた方が話が早いこともありますので、何卒お含みおき願います
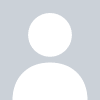
補足
焼き入れ前です。油は外部からでドリルはハイスです。 マシンはbt50番で、回転数は3500 30年前位の機械です。あら加工はラジアスエンド とラフィングエンドはラフィングエンドの方 がよいですか? ラジアスエンドとラフィングエンドでは同じ 時間で削れる体積はラフィングの方が大分 上でしょうか?ラフィングエンドはなかなか チッピングはしないのでしょうか? プレス金型の加工ではピン角のフラットエンド でないとまずい部分は何かありますか? ラジアスで対応出来ない部分って何か ありますか? ありがとうございます。プレス金型で多い座繰り加工 なら底部にラジアスエンドのRが付いても問題 ないですよね?ラジアスエンドとフラットエンドは 同じ超硬でも加工速度が大分違うのでしょうか? それとも違うのは切込み量でしょうか?
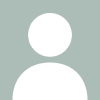
G83、G73の選択も、ドリル径、(工具)、切削液供給との絡みがあり、それ全部を開陳し人頼みするより、ご自分で試しつつ見出されるのが吉。 安全側から様子を見つつ追込めばよいのです。放電加工あれば行過ぎ折損の現物救済が可能、無ければダミー材で試す。 SKD11はプレス金型と思うが、多量にガリガリ削る必要ありますか? モールド金型でもSKD11は小さいのが多いハズ。 超硬ラフィングエンドミル 高回転、高送り、低切込み、の条件。極限では機械限界みきわめ。 切粉排除の問題。 これも人頼みしないが吉。 加工素人の嘘吐きに質問者も気付き無視してもらえた例。二人掛りでようやく。。。 http://mori.nc-net.or.jp/EokpControl?&tid=309073&event=QE0004 実技から離れるほど付け入るスキが増すので、具体例を示します。 やはりSKD11に限っては大物はほんと少ない。 https://www.nc-net.or.jp/company/87724/product/detail/59913/ SKD11 マシニング加工 t=35 230×230 削り残り代5mm http://www.etaico.com/s/ja/2/product/Rubber-mold-343729.html SKD11 200 X 200 X 80 持つに苦労しない重さとサイズ。大きさの割に加工量は少ない。 http://www.protec2003.co.jp/case/ 350x300x40 SKD11の焼き入れ硬度HRC60のワイヤー加工 屑量が増えるくり抜き加工はワイヤ。ハエが止まる程のろくてもエンドミル加工とタイマン勝負! 焼入前/後はどちらも可。段差を付けると加工速度が落ちるので、先にフラット板でくり抜き。 削る時間の短縮もよいけど、その効果如何? 金型は少量生産の代表格。段取りで機械稼働と作業工数を食われる方が多いこと屡々。 実際にその割合を計り、優先順位付けして取組むべきなのです。 もうひとつプログラムでの工夫 途切れた続きを、、と再見すれば、回答(4)が登場され、その通り。 http://omonosenban.sblo.jp/archives/20090226-1.html 深穴の仕事はワークによっては加工時間が40%も短くなりました。 これ役立つと思いますか? ならマクロの勉強を頑張ってください。 金型でないワークで数モノ、千個ほど穴の蜂の巣状の加工には、同じ工夫をやってます。 しかし金型加工ではやる気になりません。取付のタップ穴、バカ穴、パイロット穴等が同数ぐらい。 時間短縮効果はしれてます。なのにSKD11は条件追込みが難しい。 人間誰しも1日24時間のうちアタマを働かせられるのは数時間。何をやるやらないは取捨選択しなくては。
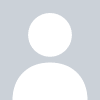
補足
ありがとうございます。プレス型です。座ぐり 加工や逃がし加工のときですが仕上げ以外は超硬 ラフィングエンドでやればいくらか 時間短縮になるか?と思いました。
補足
ありがとうございます。数ものの場合は 取り組みたいと思います