- ベストアンサー
※ ChatGPTを利用し、要約された質問です(原文:思いこみ不良について)
思いこみ不良について
このQ&Aのポイント
- 電機機器部品の設計、製造において多発している不良の原因として、「思い込みによる作業」という要素がある。
- 思いこみとは、単なる言い逃れではなく、人の感情によって生じるものであり、なぜ思い込んでしまうのかを知りたい。
- 良いアドバイスをいただきたい。
- みんなの回答 (11)
- 専門家の回答
質問者が選んだベストアンサー
- ベストアンサー
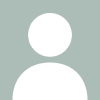
noname#230359
回答No.8
その他の回答 (10)
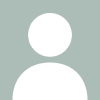
noname#230359
回答No.11
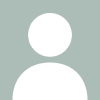
noname#230359
回答No.10
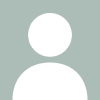
noname#230359
回答No.9
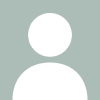
noname#230359
回答No.7
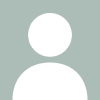
noname#230359
回答No.6
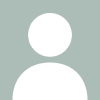
noname#230359
回答No.5
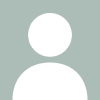
noname#230359
回答No.4
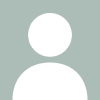
noname#230359
回答No.3
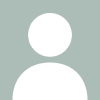
noname#230359
回答No.2
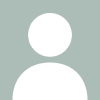
noname#230359
回答No.1
お礼
有り難う御座います。 弊社では、一応確認の後、上司が検認の形で見ていますが、殆どめくら印になっています。やはり、確実に二人目も確認するシステムが必要だと思います。 因みに、弊社では御社のように自分のミスを静粛に受け止めるのでなく、何かしら他人の問題点を見つけて、人のせいにすることが多くあります。この風習も、変えていく必要が有ると思っています。 御社がどの様に、社員一同の意見が一致したいのか宜しければ、ご教授下さい。