- 締切済み
微細部品の供給組付け No.43877 No.43902 の続き
- 微細部品の供給組付けについて悩んでいます。必要な変更を加えるために板状部品を挿入し、熱溶着シートで固定する方法を検討しています。タクト7秒での自動化を目指しており、供給方法や組付方法について悩んでいます。また、打抜の向きと組付けの向きが合わないため、解決策を模索しています。
- 2部品同時姿抜き挿入ガイドを使用した組付に絞り、公差的に圧入気味に挿入する方法を模索しています。ただし、変形や途中で止まることがないような対策が必要です。調芯性を持ったコレットを使用するアイデアも考えましたが、異形の部品では難しいと思っています。
- 質問文章では、微細部品の供給組付けに関する悩みや新たな問題について述べられています。また、社長からの指示によりタクト計算が変更され、2部品同時姿抜き挿入ガイドを使用した組付を検討しています。公差的に圧入気味に挿入する方法や挿入ガイドの構造についてのアイデアを求めています。
- みんなの回答 (10)
- 専門家の回答
みんなの回答
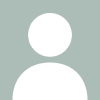
> 圧入気味に入れる挿入ガイドの構造や公差をどうするか。センターリングできるバネ構造の > イメージはありますが、これを具体的に簡単にやるにはどうするか。良い案が浮かびません。 ですが、小生は、圧入気味にでなく、最小の隙間での提案です。 >> その時の注意点は、“倣う”時に、押す力の方向と穴の淵が45°以下が・・・ > 色々な角度の意味が分かりませんが、倣って押し込まれているので、成型品の直前の ストレート部に到達しているはずなので、必ず0度になるはずと考えておりますが、何か > 違うのでしょうか? テストが簡単にできないなら、段ボール紙ではなく固い紙で、良く似た形状をカッターで 切り、穴とパーツを作り、小生が記した 今回の成形品の穴に、パーツが必ず片方側に入る位置関係(反対側は、穴の角に乗り上がって いる状態)から、パーツが入った姿抜き挿入ガイドを徐々にパーツが穴に入っている側に移動 させ、穴の淵にパーツ端面が当たると、その次は穴の淵にパーツ端面が“倣って”移動して、 全体の隙間が無くなった時に、穴に完全にセットされるとなります を、パーツを指で上から軽く押してから、横にスライドさせてをテストしてみてください。 記載内容が解ると思います。 >> パーツセットの成形品冶具を別にして、成形品を移し替える。・・・ > 移し替えは精度悪化を招くので避けたいと考えています。 > 最初に書いたように成形品は外装シリコンで絶対的に基準が無いので、移し替えたら > 精度が出ません。 > そこで、サーチピンでもう一度成型品を位置出ししていると思うのですが、 成型品は表層が > シリコンで滑りにくいため、別に超低圧のコンプライアンス+ロック機構が必要になり、 > 干渉逃げも含め、機構が非常に複雑になるので、社内では却下されました。 > それとタクトは移し替えている分長くなってしまうと思うのですが。 そう思うなら、その様にしてください。 但し、タクト計算時の成形品セット冶具の動作と運用方法は、確実に確認して計算をしてください。 止めなくてよい、セットできたら、上下の位置関係でスル―となるから。 固い紙で、セット冶具等をイメージしながらテストすると、判ります。 先ずは、一つのパーツ毎に、記載仕様でセットし、抑えてパーツが穴に沈み側へ動かす。 どのように動かせは、穴の淵とパーツ端がすべり、パーツが穴形状に倣って動作し、 穴に落ちるかを確認します。 そして、セット冶具の穴形状又は公差を決めます。 先ずは、パーツ一つづつ行ない、共通する押し方向が見つかれば、一度に二つ組付けとなります。 以上の内容ができなければ(元々無理なパーツ形状なのか、経験がなく見つけ出せないのか、 大小パーツ同時組付が必達との考えなのかも含めての内容)、画像処理で行なってください。
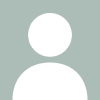
カムを使用した組立機と、その試作方法は、一定の定型ルールがあり、手でのテスト重要です。 大昔は、画像処理がなかったので、カムが主流での組立なので、手でのテストで成形穴にパーツ が上手くセットできれば、装置構想は概ね完成です。 (中昔?、セット冶具に原点マークを付け、浜松ホト***さんのセンサで原点マークを 読み取り、それを基準に調整ができる、組立職人に負担をかけない調整冶具を手掛けたこと がありますが、その環境より今はずっと良いのではないでしょうか?) 今回の成形品の穴に、パーツが必ず片方側に入る位置関係(反対側は、穴の角に乗り上がって いる状態)から、パーツが入った姿抜き挿入ガイドを徐々にパーツが穴に入っている側に移動 させ、穴の淵にパーツ端面が当たると、その次は穴の淵にパーツ端面が“倣って”移動して、 全体の隙間が無くなった時に、穴に完全にセットされるとなります。 その時の注意点は、“倣う”時に、押す力の方向と穴の淵が45°以下が望ましいが、60°でも テスト結果では可です。 しかし、0°は無論、8.5°や11.3°でも倣う方法への力が生まれない場合が出てきて、テスト での見極めが大切です。 (ねじが自然では緩まないのは、ねじ傾斜角度/リード角の方が、摩擦係数をactan化した摩擦角 より大きい理由と同じで、摩擦係数 0.15の摩擦角は8.5°、摩擦係数 0.2の摩擦角は11.3°が 示すように、穴の淵とパーツ端面の表面状態で摩擦係数が変化し、形状や大小パーツ同時 セットの要素もあり、テストでの見極めが大切です) 後、もう一つ、成形品のセット位置精度維持の手法は、以下の内容で見直しができませんか? 穴明けプレスの成形品冶具とパーツセットの成形品冶具を別にして、成形品を移し替える。 パーツセットの成形品冶具と成形品の位置精度再現性は、パーツセット成形品冶具から大小 何れかの形状のセットピンを作り冶具に内蔵させ、そこに成形品をセットします。 そして成形品の廻り止めを設けた方が位置精度再現性が良くなるのであれば、他方のパーツ を、廻り止め形状にピン化させ冶具に内蔵させます。 ピンの形状精度は、鋼加工精度一杯に詰めて、ピン下部は単動シリンダが如く機構で、上下が 可能にします。 成形品がスカラにてパーツセット成形品冶具にセットされた後に、成形品をクランプさせ、ピン が下降し、姿抜き挿入ガイドがパーツセット成形品冶具にジグピンにてドッキングします。 (それか、ピンが下降しないで、そのピンが姿抜き挿入ガイドの案内ガイドとなり、ドッキング してからクランプ固定、後にピンが下降で、パーツセット待ちとするか。) そうすれば、搬送⇒穴明けプレス⇒搬送の時間を除いてのタクトタイムとなり、パーツセット 組立工程に時間が割ける。 パーツセット組立工程の冶具周囲がシンプル化して、からくり機構が仕込み易くなる。 以上のように考えるのですが、理解して頂けるでしょうか?
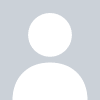
お礼
ご回答ありがとうございます。 >その時の注意点は、“倣う”時に、押す力の方向と穴の淵が45°以下が・・・ 色々な角度の意味が分かりませんが、倣って押し込まれているので、 成型品の直前のストレート部に到達しているはずなので、 必ず0度になるはずと考えておりますが、何か違うのでしょうか? >パーツセットの成形品冶具を別にして、成形品を移し替える。・・・ 移し替えは精度悪化を招くので避けたいと考えています。 最初に書いたように成形品は外装シリコンで絶対的に基準が無いので、 移し替えたら精度が出ません。 そこで、サーチピンでもう一度成型品を位置出ししていると思うのですが、 成型品は表層がシリコンで滑りにくいため、 別に超低圧のコンプライアンス+ロック機構が必要になり、 干渉逃げも含め、機構が非常に複雑になるので、社内では却下されました。 それとタクトは移し替えている分長くなってしまうと思うのですが。
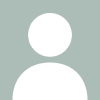
相変わらず無駄な回答が並んでるけれど > 厚みが0.75mmなら、キーエンス等のセンサにてワークが穴に嵌る確認も取れるでしょう。 こんなペラペラで小さな樹脂を検出出来るセンサは有りません 近接センサにしろ光電センサにしろ これが可能なのは画像処理装置しかない <安価な画像処理装置では恐らくムリ で、アフターさんに問う 貴殿が想定する装置のご予算は? 1千万円?2千万円? <購入部品だけでなく設計製作エンジニアリング費その他諸経費込 購入部品だけなら2百万円~3百万円で済むか? <後はサービス残業だけで作るのか? 技術的には可能でも 必ずしもキャッシュフロー的に可能とは限らない 憶測ですが ↓のようなハンドプレスと20万円~30万円くらいで治具作って http://jp.misumi-ec.com/vona2/detail/223000692060/?SpecP=223000692060 後はパートさん数名 そんなところに落ち着くのでは? タクト14秒ならそれで可能でしょう
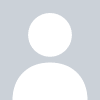
お礼
ご回答ありがとうございます。 その挿入確認は挿入時の浮きを言われてると思うので、 それであれば私自身も充分可能と考えております。 今回は社長命令で動いているので、 検討設計は開発費で落としておりますし、 ここには書けないですが、特別配慮もして頂いております。
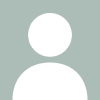
> 姿抜き挿入ガイドの当該穴公差は、成形品穴と同じ位にしたら如何でしょうか? > そして、ワークを押すと、成形品穴の(仮に縦をY横をXとすると)YとXのプラス側に必ず入り、 > マイナス側は乗り上がる状態にします。(各構成品の精度確認をして、必達です) > そして、ワークを押したまま、姿抜き挿入ガイドを(倣い)カム等で、YとXのプラス側に > ゆっくり押すと、ある位置でワークが成形品の穴に嵌ることになります。 > 厚みが0.75mmなら、キーエンス等のセンサにてワークが穴に嵌る確認も取れるでしょう。 は、理解できませんか? そして、それを > 手のテストで大小パーツが同時セットが可能ならその仕様で、別々でないと なら、 > 組付ステージを増やし別々に、問題が残るなら別の案を検討するか、虎虎虎君へ案の打診 > をするか決める段階ではないでしょうか?(だから、冒頭で、部分試作テスト段階と記載) となっているのですが、理解できませんか? 定型での組立機で、姿抜き挿入ガイドの姿抜き寸法公差を色々試し、手でワークが成形品に 入るかの確認を何回もします。 それで、形状や公差に因って、上手く行く場合と行かない場合を判断し、上手く行く場合は その定型を使用、上手く行かない場合は別のやり方で姿抜き挿入ガイドの仕様を決めるです。 こちらでは、当該の物も無いし、テストできません。(抜きのカエリとかも??ですし) 試作冶具を作って、手を駆動源として、テストをすれば、 > そのXYの動くタイミング次第で入る入らない、そういう状態になる気がしています。 の判断が付くのではないでしょうか? 小パーツは、目の形状に似ているなら、目尻又は目頭方向へ、公差ブレを考慮して、1方向でも セットは可能と思っていますが、大パーツが問題になるので、やはりセットは2工程分けかな? 一つ気になったのですが、大と小パーツのカエリが出る方法と、成形品のカエリが出る方向は 合わせる必要があると考えるのですが、大小パーツと成形品の表裏を一定にしての段積みセット だけで可なのでしょうか? 誤った段積みセットがあったら部品排除するのでしょうか?又は組立後に製品不良排除するので しょうか? カムを利用した組立ライン設計に慣れていないみたいですね。 心配な箇所は、試作を作って事前にテストするとか、調整が簡単にできるようにとかを。 それなら、他の回答者さんの記載の如く、画像処理位置出しでのロボット組付けをすれば、 コストはかかりますが、後でどんな調整も殆ど可能になり、カムを利用した組立ライン設計 に慣れていない貴殿には、画像処理位置出しの方が良いかもしれませんね。 成形品のカエリがない向きに、大小パーツのカエリがある方向が組付けば、 カエリが表にでることになり、拙いのではないでしょうか? 仕様から推測すると、溶着シート貼付けは成形品のカエリがある方向なので、反対側は、 カエリの保護がないと想像していますが、正しいでしょうか?
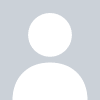
お礼
ご回答ありがとうございます。 XY動作で入るタイミングは必ずありますが、 そのXYの動くタイミング次第で入る入らない、 そういう状態になる気がしています。 カムとあったので何度もそれを行うのかなと思った次第です。 ご回答ありがとうございます。 ご指摘の通り、カムを使ったことはありません。 また、成型品はバリ方向から入れることになります。 大パーツは表裏が明確になりますが、 小パーツは逆になると分かりません。 本体の表から裏に打抜き、本体の裏から大小部品を挿入、 続けて裏から板付溶着シートを当て加熱溶着となります。 この手法で外観への出っ張り0.05以内でクリアしました。 シリコン表層があるためか、カエリは全く見られません。
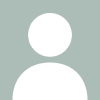
もう構想はできているのなら、後は部分試作テストをして、各部品スペックをチューニング させ、製作する段階と考えます。 > ?スカラーロボットで、短軸ロボット付吸着機構治具に投入。 単軸ロボシリンダを使用するですね。 > ?前記治具で、吸着したままスライド投入し離さずにプレス切断。 吸着したままスライド投入し離さずにプレス切断は、前回答追記課題?のためでしょうか? > ?その位置状態を維持して前記治具をリターンさせ、そこでスカラーで微細部品を組付。 タクトタイムの制限と、将来の7秒タクト化から、避けた方が良いのでは? 小生のイメージは、 更にスライド 此処で、パーツ組付け ┌───── 成形品セットB ←────┐スカラで移載 │ │ ↓(シートもセット) (成形品段積み) │ 排出←熱溶着st スカラロボット 成形品セットA⇔穴抜きプレス ↑ (小パーツ段積み) (大パーツ段積み) │ │ │ └───── 成形品セットC(将来用) ←┘スカラで将来移載 将来更にスライド 此処で、パーツ組付け(将来用) かな?、スカラの拘束時間とハンドの構成は貴殿で更に要確認ですがね > ?続いてその上に熱溶着シート(板付)をスカラーで組付。 小生は、上述イメージでそのようにです。 > ?さらにスライドして専用ヘッドで熱溶着。 ?と同じく。 ?再度スライドしてスカラーロボットで排出。 > 画像で記録を残したり、検査をしたり、出荷荷姿に整列が不明なので、コメントなし。 課題に関しては、 > ? 吸着保持プレス切断の廃材が上に出るが上手く排出できるか? バキュームですれば、樹脂なので可能と思いますが、上抜きの必然性が今一解りません。 > (出来ないと反転機構が必要になり、そこでの受け渡しによる精度悪化で成り立たなくなる) 上述イメージフローの観点から、理由が良く解りません。 元々、画像合わせは考慮外の記載なので、回答(5)の中断位に、受渡し冶具の構想案を示し ていますが、手動でのテストで大小パーツが同時セットが可能ならその仕様で、別々でないと なら、組付ステージを増やし別々に、問題が残るなら別の案を検討するか、虎虎虎君へ案の打診 をするか決める段階ではないでしょうか?(だから、冒頭で、部分試作テスト段階と記載) > ?精密組付けの方法 回答(5)の中断位に、受渡し冶具&倣いカムを案として記載しております。
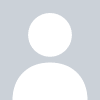
お礼
ご回答ありがとうございます。 ?その位置状態を維持して・・・は、 吸着治具で抜いた位置を吸着保持して維持したまま、 スライドさせることで組付位置を保障するためです。 ? 吸着保持プレス切断の廃材・・・は、 逆側(上)から切断すると2色成形の表層シリコン側が、 どうしてもバリになってしまうため、下から切断になるということです。 また、7秒タクト時は、もう一台と言われているので、 今回は、確実に14秒に入る方法を考えればいいです。 <逆に質問ですが> 倣いカムとはどういう機構なのでしょうか? 振動挿入併用ということになるのでしょうか? 質問が分かり難いと思い補足しますが、 倣いカムだと、入るチャンスは一回あるかないか。 そうなってしまうと思うのですがいかがでしょうか?
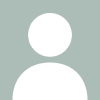
おい!虎!最近、また投稿してくるが、他人批判かい。 そして、この質問関連の初期投稿で、勿体ぶった記載をして、見ただけかしているだけで、 中身がないから、高見の見物だろう。それだけの人間、いや虎と考えるいい機会。 (この森の主旨である広く情報を求める意図が理解できない奴と思えば、……) さて、タクトが14秒になったのは大きいですよ。 姿抜き挿入ガイドの当該穴公差は、成形品穴と同じ位にしたら如何でしょうか? そして、ワークを押すと、成形品穴の(仮に縦をY横をXとすると)YとXのプラス側に必ず入り、 マイナス側は乗り上がる状態にします。(各構成品の精度確認をして、必達です) そして、ワークを押したまま、姿抜き挿入ガイドを倣いカム等で、YとXのプラス側にゆっくり 押すと、ある位置でワークが成形品の穴に嵌ることになります。 厚みが0.75mmなら、キーエンス等のセンサにてワークが穴に嵌る確認も取れるでしょう。 如何でしょうか? 14秒タクトなので、ポピュラーな成形品をタクト送りしてから、ワークを成形品穴にセット が可能になり、簡単な手法でのアドバイスができることになりました。 樹脂成形品に明ける穴の絶対位置精度は、いくらでしょうか? 樹脂成形品なんで、シリンダを使用した冶具プレスで良いんですよね。 樹脂成形品の穴明け工程とワーク嵌め込み工程は、できるだけ同じフィード機構でがベータ― であるため、多少頭に入れて、計画したほうが良かろうと考えます。 ライン構想は、一応練っていた方が良く、 例えば、プレス工程の樹脂成形品は、フィード機構送り 嵌め込み工程への振り分け送りは、スカラロボット? 嵌め込み工程でのワークセットも、同じスカラロボット? 嵌め込み工程の樹脂成形品は、フィード機構送り 送り後に熱溶着≪熱溶着1台なら、将来2ライン分の処理形態となる≫ となりそうですかね。
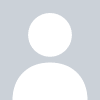
お礼
ご回答ありがとうございます。 ?スカラーロボットで、短軸ロボット付吸着機構治具に投入。 ?前記治具で、吸着したままスライド投入し離さずにプレス切断。 ?その位置状態を維持して前記治具をリターンさせ、 そこでスカラーで微細部品を組付。 ?続いてその上に熱溶着シート(板付)をスカラーで組付。 ?さらにスライドして専用ヘッドで熱溶着。 ?再度スライドしてスカラーロボットで排出。 こういう流れで考えております。 <課題> ?吸着保持プレス切断の廃材が上に出るが上手く排出できるか? (出来ないと反転機構が必要になるのと、 そこでの受け渡しによる精度悪化で成り立たなくなる) ?精密組付けの方法
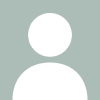
質問者さんが、後(ご)の先(せん)、アフターユーさんと一生懸命に対話してるので自分はしばらく休憩しますね。事の成り行きを見守って見ます。 後(ご)の先(せん)、アフターユーさんが、口からデマカセ男と判って愛想を尽かせたら呼び出して下さいませ。 もちろん、後(ご)の先(せん)、アフターユーさんの真摯な意見により成功されれば、お喜びを申し上げます。
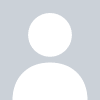
お礼
ご回答ありがとうございます。 質問を絞りましたので、 アイデアがありましたら、ぜひお知恵をお貸しください。
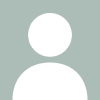
前質問 No.43902にて、 > 最終寸法が決定しました。 > 小さい方の穴 長手4.80±0.07 短手2.02±0.07 > 小さい方の挿入部品 長手4.69±0.07 短手1.94±0.07 > と非常に厳しいものとなりました。 の記載で、訳の解らない回答者から、最終製品での性能確認まで踏み込んだ記載がありました。 本来、成形品の部品精度や板状パーツの部品精度は、製品の性能や品質に影響があるため、 部品組み立てメーカーだけでは公差は決められません。 製品メーカーが試作をし組付け性確認して、組付け後は加速試験を何種類かして、公差を 含めた仕様を製品メーカーが決定するため、公差に対しては問題ないですよね。 但し、 > ……と非常に厳しいものとなりました。最悪の場合、無理やり押し込むことになります。 と云う質問者さん記載は、組立ての設備性能又は仕様が、そのようになるとの記載ですよね。 だから、小生は、“成形精度は、落とし込み冶具と成形品のセット方法や工夫にて、 何とかなる物ですよ”と記載したまでですよ。 また、組立費に関するコスト面や組立安定性に関する品質面で、製品穴の一部を形状変更や 公差変更するニーズが生じた時に、製品メーカーと部品メーカーが合議すれば変更可能となり 組立性改良理由にて、成形品図面が改訂手順だと思うのですが、間違いはないでしょうか? 小生は、前質問 No.43902にも記載しましたが、 ア)マガジンからファミリーに移し替え 追加部品とファミリーでテープ供給(キャリアテープの如く、両端送り穴付き仕様にて) ↓ イ)位置決めは姿穴に落とし込むしかないことと、打ち抜きっ放しのため 成形品も板状パーツも、全く面取りがない ↓ ウ)例えば姿穴落とし込み付き冶具を、精度よく成形品にセットできる仕様とする 上層部;ファミリーでテープ供給が、流れ方向に直線か、上方へクランクしテープ排出 中層部;姿穴落とし込み付き冶具が、数個水平にくるくる寿司C/Vの如く移動 下層部;成形品が直線で流れる(ワーク吸着穴内臓にて、中層部冶具からワーク抜き出し) の3層構造で、上層部から中層部へワーク落とし込み、下層部の成形品にワークセット ◎ 姿穴落とし込み付き冶具と成形品のセット&リセットの位置再現精度 ● 姿穴落とし込み付き冶具の姿穴間口の面取代 ○ ファミリーでテープ供給する(送り)精度 ※ 姿穴落とし込み付き冶具の姿穴でワークが引っ掛らない押し込み機構 にて、各工程が精度的に成り立つ、精度補正目的の画像は必要なしの場合、 7秒で組立装置をカムを利用して製作仕様が、優先順位の一番です。 ですが、スカラロボットで高速化を図る案でも、アドバイスしますよ、特に設備仕様でね。 できれば、工程順での記載をした方が解り易く、アドバイス等が、ちぐはぐにならなくて 宜しいと思います。 ◆ 成形品の打ち抜き工程 成形品のフィード方法 ↓ 成形品の移動方法とツール ↓ ◇ 成形品と板状パーツ組立工程 成形品のフィード方法 板状パーツと他の供給方法 を少し明確に、しかも工程順に記載すればです。 テープ両端に送り穴がある類似例 http://www.ady-jp.jp/category/1397263.html 俺も含めて、上述の◆印の内容記載か、◇印の内容記載かで、混乱をきたしています。 できれば、質問追記で、暫定案でも記載してもらえれば、具案が記載し易いのですがね。
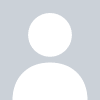
お礼
ご回答ありがとうございます。 組立性改良が隙間アップになる場合、 却下されるのは間違いありません。 そうでなければ大丈夫です。 ア)社内でマガジンからテープに移し替えだけは考えていません。 外注で、マガジン、テープ、どちらかで供給されるつもりです。 混乱させて申し訳りません。 質問を◇に絞りましたので、 ぜひお知恵をお貸しください。
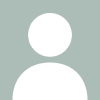
ぜんぜん。 機械は上部がフリーな空間になるダイイングンマシンが使いやすい。 http://www.nidec-shimpo.co.jp/prs/02/000054.html http://toscom.cocot.jp/abt-press_machine.htm 中古もあるが数少ない。 http://www.zenkiren.net/machine_detail.php?m=44752 旧式のパワープレス機も後方に30度傾きます。 http://ja.aliexpress.com/item/inclinable-power-press-mandrel-press-angel-pressing-machine/613821898.html?spm=2114.52010608.4.9.U6O2wc 横型プレスは打抜きと組立作業を同時に行う複合で使います。
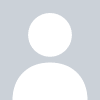
お礼
ご回答ありがとうございます。 300角程度のダイセットを使い、 エアーシリンダー抜きで今の所は成功しています。 問題は、今回の自動化の際、 吸着台で型内に移載してそのまま抜くことと、 (その精度を維持して型から精密組付ポジションに移動させるため) 型の天地が逆転してしまうことです。
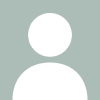
未だに続いてるんですねぇ 未だに返答頂いていない項目 装置に使える総投資予算 総受注数量及び年間受注金額(年間数百万個でも1個1銭とかだと????) 今後何年分の受注残が有るのか?もしくは受注見込みがあるのか? よーするに投資回収可能金額 話は変わるけど、今日のテレビ朝日「スゴイデスネ視察団」 http://www.tv-asahi.co.jp/shisatsudan/backnumber/2016/0037/ コンビニドーナッツ製造現場見ましたか? それなりに機械化して自動フライヤとかでドーナッツ揚げてるけれど 重要な箇所はパートさんによる手作業 見た目ロボットでもできそうな作業でしたが 恐らく敢えてロボット化しないのだと思います その理由は恐らく投資回収できないから(流行物なので生産数量が確保できない) 本件もスマホ製造なら生産期間はせいぜい長くて1年 <投資回収予算は少ないであろう 来年は少々の追加改造(ソフトパラメータの変更のみとか)で済めば良いのですが 今年5百万で作って、来年はそれを3百万で改造しなければならなかったら? 無間地獄の始まり始まりぃ 例えば予算が8百万しかないけれど設備屋からの見積回答が1千万とかだったら 機械構造や仕様を変更すれば2~3割は安くできるであろう でも、半額にするのは至難の業、7割引きにするのは不可能 半額にする一番簡単な方法は 各機器単体購入して設計、ソフト、組立、エンジニアリング費は自分一人で サービス残業だけでやること サービス残業だけでやるのは簡単だけれども、それは禁じ手 コンビニや郵便、保険業界で言う自爆営業と同じ
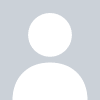
お礼
ご回答ありがとうございます。 社長の指示であまり書きたくないのですが、 開発要素が多いので、設計や組立費用を一部調整すると言っています。 これ以上はご勘弁願います。
お礼
ご回答ありがとうございます。 圧入ではなかったのですね。 隙間があるとすれば、 XYを止めるタイミングはいつなのでしょうか? 社内で議論して、モデルも作ってみましたが、 理論上は良い位置で止めないと入ることなく通過しますね。 ご回答ありがとうございます。 社長にこれまでの経緯を説明した所、 そんな不安定なリスクのあるやり方は止めろ。 今一番確実な画像で行けと指示が出されました。 金の心配はするなとも。長らくお騒がせしました。