- 締切済み
タッチプローブを使用した原点測定ミス多発!
- タッチプローブを使用した原点測定でのミスを解消する方法について教えてください。
- タッチプローブの半径移動を忘れずに行うための確認方法を教えてください。
- タッチプローブを用いたワーク原点測定においてミスを防ぐための技術的な方法を教えてください。
- みんなの回答 (7)
- 専門家の回答
みんなの回答
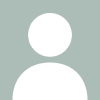
半径移動を忘れてしまうということはプローブ当てたところをゼロにして、その後半径分移動させて再度ゼロにするってことでしょうか。 当方OSPなんですが、原点設定の時に直接半径分を設定出来るので、あらためて移動する必要がありません。 例えばXプラス方向に当ててゼロにしたい場合に、プローブ当てたところで直接「-3」と設定することが可能です。 他のNCは出来ないのでしょうか・・・。 出来ないとなるとMDIで「G92X-3.」とする事も出来ると思いますが、これは少々危険ですね。(入力ミスで動く可能性がある為) ちなみにいくつか回答にあるOSPのマニュアル計測は私も使っています。 私の勘違いかもしれませんが、マニュアル測定と言えば手動で測定するヤツの事ですよね?? 自動原点設定の機能とは別のものですよね??? あれれ?特にオプション追加した覚えは無いのですが・・・。 それは置いておいて・・、 手動にてこの機能を使う場合においてもそれなりに注意は必要ですね。 端面測定時にプローブを当てる方向(X+ X- Y+ Y-)を指定する必要があり、この方向を逆にしてしまうと半径どころか、直径分間違えてしまいます。 OSPについて書きましたが他のNCでも同様の仕組みであった場合、同様の注意は必要かと思います。 でも、まあ便利です。特にゼロ以外の数値に設定する時や、丸のセンターを出す時、加工後の測定など半径を意識しなくてすみますから。 先に言われている半径補正分のパラメータはそれぞれの方向のプローブの倒れも補正されるので、プローブが振れていても正確に出せるという利点もあります。 長々と書きましたが、 結局どのような方法で原点を出したとしても、後で他の方法を使って原点の確認は必要であると私は考えます。 それは、やはり実際に定位置に位置決めしてサシなどで確認することです。 誰もがMCの基礎として習うであろう基本だと思います。 特に半径分のミスであれば測定した基準面に位置決めして目視程度で発見できるかと思います。 また、一度に複数のせる製品であれば、この作業自体をプログラムにしてしまえば確認作業の負担も軽くなる(面倒じゃなくなる)かと思います。
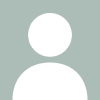
OSPのマニュアル計測を使っていますが、此は大変素晴らしいオプションです。 約4年マシニングセンターを使っていますが、計測忘れや測定ミスは発生した記憶がありません。(只単に忘れているだけかも^^;) 誰が使っても、計測ミスが発生しにくい点では一押しです。 後、特定の場所に加工原点を持っていく場合は、メモ用紙に作業手順を自分で書いて張ってあります。 >特定の場所に加工原点を持っていく場合は、 誤解があるといけないので追記します。 端面や測定の中央値以外で、図面の原点とは違う数値や0やプローブの半径以外の数値を入力する場合です。
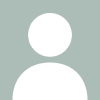
物理的な対策の前に、段取りの一通りの作業として 半径移動する事を当たり前の様に、体に染み込ませる事が大事だと思います。 とくほんさんの仰られてる通り、指差呼称大事ですよ。 >>めんどくさい 所詮は人間のすること…。 凄くよく分かりますけどね。(^_^) 私も同じ所あります。 『タッチプローブの半径移動忘れずに!』 紙に書いて機械に貼っておけば、これだけでも効果はあると思います。 お金も掛からないし…。
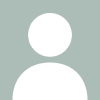
質問者さんの質問履歴を拝見しました。 技能士を目指されているようですね。 それなら一言。 「指差呼称」 意外に効果は大きいです。 現在されていないのでしたら、試してみて下さい。 「プローブ径入力ヨシ!」
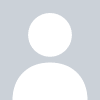
お礼
どんなことでも指差確認が第一であること。 これをどんな状況でも理解し、実践することが大事なんですが、しかし所詮は人間のすることですから・・・ と、これは言い訳にしかなりませんね。
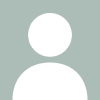
NCの仕様で、画面のメニューとの対話形式で原点を設定するというものがあり、それの便利な点のひとつが、あらかじめプローブの径補正をパラメータで設定しておき、普段の原点設定作業ではいちいち径補正を考慮して数値を入力する必要がなく間違いもなくなるというものです。 自動計測のキャリブレーションと同様なしくみですね。 OSPで「マニュアル計測」という特別仕様です。 他のコントローラでも特別仕様と思います。
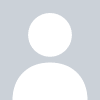
お礼
正直、私では理解し、設定することは難しいと思いますが、職場の人に提案して、実践してみようと思います。 この方法がうまくいけば、特別何かを購入することがなく、すぐに使えそうですね。 ありがとうございます。
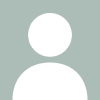
私は使ったことありませんが、「エヌティーツール」の「ゼロマスター」はプローブの径補正が不要です。 http://kikai110.jp/tinyd1+index.id+4.htm 大昭和精機にもあります。 「3Dマスター」「3Dマスターミニ」 http://asahi.astt.co.jp/gnet/s3/sa16.html#anchor114753
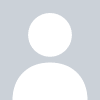
お礼
これは使えそうですね。 実際に見積もりを取ってみようと思います、ありがとうございます。
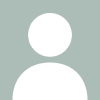
「ワーク原点の取り忘れ」・・・ よくあることです。 原点が取ているかを確認するワーク原点移動プログラムを用意されてはどうでしょうか。 ----------- O-9010 91G28Z0 G54 X0Y0 Z100. M00 Z5. ---------- 計測した後、プロープが主軸についた状態でこのプログラムを実行すれば原点がとれているか確認できます。 ワークの上面"100.0"のところで一旦停止しますので、100のゲージを差し込んで確認しています。 その後"5.0"まで下がって来ますので、半径分の処理を忘れていれば確認できるでしょう。 "5.0" まで下げる必要がなければ、実行キャンセルして下さい。 なおこのプログラムはイメージで書きましたので貴殿の業務に適したものを作成してください。 さらに、このプログラムをマクロとして登録しておけばMDI操作で実行できます。 後はアイデア次第です。
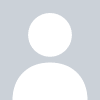
お礼
私も実際にこの方法を行っています。 では、なぜ原点を間違えたかというと、一気に5個セットして、それぞれにこの方法をやると、めんどくさい、といういい加減な気持ちになってしまうときがあるのです。 もっとも対策を立てなければならないのは、そういう気持ちをなくすことですよね。
お礼
うーん、やはり端面に当てて、ゼロにして、半径移動して、原点を入力するのと、端面に当てて直接「-2」と入力するやり方と、どちらがミスが少ないかやってみようと思います。 ご指摘のとおり、最終的に目視での確認を疎かにしているという現状をどうにかしなくてはなりませんね・・・ 皆様、どうもありがとうございます。