- ベストアンサー
コストダウンの業績評価の指標?
メーカーでの工場におけるコストダウンをどう業績評価すれば良いのか困っています。何か良い指標はありませんか。他社ではどのような指標を用いているのでしょうか。例えば、予算計画時での生産品目と実際の生産品目が違う場合など単純な計画対比ができません。こうした場合、その品目のコストダウン実績をどうやって算出すれば良いのでしょうか。当社は、中小企業ですのであまり良い経営データが手元にないのですが・・・。 何か、ヒントでも良いので教えてください!
- みんなの回答 (3)
- 専門家の回答
質問者が選んだベストアンサー
そのコストダウンをせずに従来の方法で製作したら、 幾らコストが掛かったかを算出し、これから、 コストダウンでダウンしたコストと、コストダウンする為に掛かった費用 を 引くのはどうでしょう。 もちろん、コストを1個あたりで計算するなら、 コストダウンする為に掛かった費用も生産個数で割る必要があります。 電子機器のように部品数が多い物は、単純計算の方が 精度良く出る場合がありますが、これは業種によって違うので なんともいえないかもしれません。 (たとえば、回路規模のコストダウンは、基板の面積から算出してしまう) (生産工数のコストダウンは、生産に掛かる作業時間から算出してしまう。 熟練工が必要な作業時間は倍で計算 といったような単純化)
その他の回答 (2)
- yotarou
- ベストアンサー率35% (6/17)
質問から量産品を造っておられると考えます。基本的な考え方としては原価計算を実施することだと考えます。標準原価を設定し、品目別に標準に対して実績がどうであったかを比較することで計画値に対して実績がどうであったかが捕らえられると思います。標準を設定するに当たっては材料費、労務費、及び経費について設定が必要です。労務費を考えるときに標準時間の設定が問題になりますが、実績を収集し標準としても良いのではないでしょうか、徐々に精度を上げていくといったスタンスで十分だと思います。そしてPDCAを回す基本を回してゆけば改善につながるものと考えます。
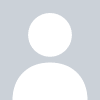
お礼
yotarou様、ご回答ありがとうございます。 御礼が遅くなり大変失礼致しました。 確かに >実績を収集し標準として 良いのだと思います。地道な作業ですが、徐々に 精度を上げてゆくしかありませんよね。 がんばります。
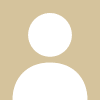
生産管理のような部門の者ではないので、勘違いがありましたら恐縮です。 コストダウンではなく、VEという観点から捉えてはどうでしょうか。 VEを行うには新しいアイデアが必要です。 VEのアイデアによって結果的にコストダウンができると考えれば、そのアイデアこそが評価の対象となります。 よく企業では「改善提案」という制度を設けています。 そして、改善提案によって導かれるコストダウンは、その提案者の業績となります。(報奨金を設けるところもあります) アイデアを変化点とすると、コストダウンを"その原因も含めて"量的に捉えることができると思うのですが・・・
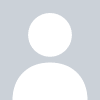
お礼
Speedmaster様、貴重なご意見ありがとうございます。 VEとはValueEngineeringのことですね。 確かに世の流れはものの値段の算定から付加価値の 判定へと動いています。良い物は高くても買う、悪い物は 安くても買わないといったように・・・。 違った観点からもいろいろ考えてみたいと思います。
お礼
早速ありがとうございます。 生産工数を時間でという考え方については試行しているのですがサンプル採取と標準時間の決めをどうするかでやはり頭を悩ませています・・・。