- 締切済み
上手な熱間樹脂埋めの方法
- 熱間プレス機を使用したベークライトを使った樹脂埋めの際に、樹脂と試験片の界面に隙間ができる問題が発生しています。この問題に対する対策方法や注意点を知りたいです。
- 現在、試験片をプレス機にセットし、ベークライト粉末を充填した後、加圧と除圧を2から3回繰り返し、ガスを抜いています。その後、規定圧力まで加圧し、6から7分間保持し、除圧後に試験片を取り出して水中冷却しています。しかし、研磨後に樹脂/試験片界面に隙間ができ、面ダレが発生しています。
- ベークライト使用時に樹脂と金属間に隙間ができない方法や、ガス抜きの方法、試験片の準備方法など、熱間樹脂埋めの際に注意すべきポイントを教えてください。
- みんなの回答 (2)
- 専門家の回答
みんなの回答
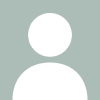
似たような業務を行っている者です。 1.まず研磨紙にて#400くらいまで研磨する。 2.出来れば試料を超音波洗浄する。(隙間のごみを除去する) 3.低粘土の瞬間接着剤(アロンアルファ)を隙間の出来ている所に塗布 4.硬化促進剤があるので、スプレーすれば瞬時に硬化 5.後は、通常の研磨を行う。 ・100%とは行かないですが、窒化等の剥離しやすいSampleには効果大です!!
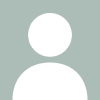
>>組織観察の為に研磨すると 良く作りました 熱をかけるのはやめたほうがいい どうしても内部応力がかかるから 常温硬化のものがいいです 境界での面ダレは樹脂の柔らかさによって起きる場合もあるので(魔境みたいに削れる) 完全には防げません 透明レジンがお勧めです 高いけど 切ったり 磨いたりする時に 中が見えるので失敗がない なんか難しく考えすぎです 2液タイプの常温硬化タイプのモノは 固まるのにだいぶ時間がかかるので 混ぜるスピード なんて 適当でいいですし ドラフトチャンバーなんかいりません 脱泡に真空器があればベストですが なくてもできます 熱をかけるタイプだと 樹脂は表面から固まりはじめるので 内部応力は外に向きます 2液タイプのモノは 化学反応で発熱するので一様に温まり一応に冷えるので応力は発生しにくいです 境目ができにくいですよ http://www.geocities.jp/tarokun_studio/howtotop.html 現状モデルをhttp://www.sanyo-chemical.co.jp/product/sanmodur/jpn/properties.htm で作ってますが 目分量で5:5 適当にねって固めてます ナットなんか埋め込んで使ってますよ 試験片じゃないので鏡面まで磨きませんが 150度も暖めると 常温との温度差は130度近くあり 熱線膨張が無視しできないです 比熱も金属と樹脂では違うので 応力がたまりやすいです
補足
回答有難う御座います。 応力の発生や固溶ガス元素の出入りが問題になるほど 厳密なことは管理しない、という前提です。 組織観察(しかも浸炭層、窒化層深さ、表面の 酸化層の観察程度)、ビッカースやヌープ硬度測定を する程度ですので、固溶ガス元素が出入りするとか、 内部応力によって硬度が変化するとか、 どの道、検出できません。 それに冷間はガス抜き等、それなりに熟練が必要な上、 樹脂の臭いがきついのでドラフトチャンバーも必要です。 混ぜるスピード、硬化速度等、なかなか標準化が難しい・・・ 手順書も作らないといけない・・・ と言うことで、ベークライト使用でメッキは使用しないで、 手早く次々と作製して、それでいて隙間が出来ない、 という方法を探しています。 樹脂が先に削れてしまうことで面ダレするのは ダミーもいっしょに樹脂埋めするとか研磨荷重を落とすとか、 ある程度対策可能ですので、OKです。