- 締切済み
※ ChatGPTを利用し、要約された質問です(原文:鋼板削りの極意を教えて!!)
鋼板削りの極意を教えて!!
このQ&Aのポイント
- 2mx1.5mT80mm位のSS400又は、S50Cの鋼板を削る際に厚さ決めや反り問題があります。良いカッターや加工方法を教えてください。
- 鋼板削りの際に反りが出てしまう問題があります。カッターセット換えをしてもなかなか仕上がらず、納期にも間に合わない状況です。助けが必要です。
- SS400又は、S50Cの厚さが80mmの鋼板を削る際に問題があります。厚さ決めや反りの問題に対処するためには、良いカッターや加工方法を採用する必要があります。
- みんなの回答 (4)
- 専門家の回答
みんなの回答
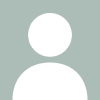
noname#230359
回答No.4
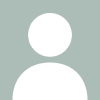
noname#230359
回答No.3
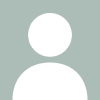
noname#230359
回答No.2
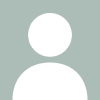
noname#230359
回答No.1
お礼
加工何とか上手く行きました。0.05mmに治まりました。確かに仕上げ加工の時フライスの刃を1枚 で加工(ワイパーチップ)だと上手く行きました。他のカッターでいろいろ試してみたのですがやはり厚さでませんでした。殆どノークランプでソリッドバイスそえただけみなさんのおかげで何とかうまくできました。又問題がありましたら、よろしくお願いします。