- ベストアンサー
※ ChatGPTを利用し、要約された質問です(原文:セラミック粉の粒径とバインダ添加量の関係?)
セラミック粉の粒径とバインダ添加量の関係について
このQ&Aのポイント
- セラミック粉の粒径とバインダ添加量の関係について調査しました。一般的に、粉の粒径が細かくなるとバインダ添加量は低減する傾向があります。
- また、粉の粒径が細かくなると比表面積が大きくなりますが、この場合でもバインダ添加量は低減することが多いです。
- しかし、粒径や比表面積だけでなく、他の要素も関係している可能性もありますので、具体的な条件や目的によって最適なバインダ添加量を判断する必要があります。
- みんなの回答 (3)
- 専門家の回答
質問者が選んだベストアンサー
- ベストアンサー
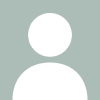
noname#230359
回答No.2
その他の回答 (2)
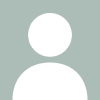
noname#230359
回答No.3
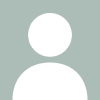
noname#230359
回答No.1
お礼
ご回答,ありがとうございました。 元々バインダーを過剰気味に添加していたのか,最適量を添加していたのか,逆に不足気味だったのか,それによっても状況が変わるため,粒子径が変わったからと言ってバインダ添加量をすぐに変える事は無いのでは,という理解でよろしいでしょうか。 ちなみに私がバインダ量にこだわっているのは,焼成後の残炭等の問題があるため,できるだけバインダ添加量を減らしたい,という思惑があるためですが,一般的にどちらに添加量を動かすものなのかが知りたかったためでした。