- ベストアンサー
NC旋盤用オートローダーの使い勝手について
- 最近、加工現場の自動化について検討するように上司から言い渡されました。色々勉強している最中、NC旋盤用のオートローダーに行き当たりましたが、現在の製造業界で自動加工の主流がライン工程や各種ロボット使用になってきているため、あまり情報がありません。
- 実際にNC旋盤用のオートローダーを使われている方、加工現場でオートローダーが動いている様子を知っている方がおられましたら、使い勝手や不具合、生産性について意見を聞かせていただけないでしょうか。
- ローダーに長さを揃えた母材をストックしておいて、その母材寸法に合わせた製品をプログラムだけ組んで流しておけるならば、加工現場の効率はあがると思いますが、実際には寸法出しなどの問題からそういった使い方は難しいのではと想像しております。
- みんなの回答 (4)
- 専門家の回答
質問者が選んだベストアンサー
- ベストアンサー
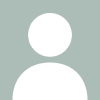
自動ローディング装置は、小ロット対応も随分進んだとは言え やはり専用機的な色は強くなりますね. ガントリータイプの様なアームでワークを掴むものは ワークサイズに合わせて爪を拵えなければなりませんし、 より構造の単純なシュートタイプにしても 何かと調整は必要で、しかもワーク形状が限られる事になります. ローダーだけで何百万とか1千万とかかけられるなら、 画像認識装置を組み込んだ産業用多関節ロボット的なものを使って、 ティーチングさえすればとくに部品交換などは無しに行けるのかも知れませんが、 工賃が限界まで絞られている昨今、一般の工場では費用対効果の面で疑問符が付きます. 私の勤め先にも組み込みガントリーローダー付きの古い旋盤が何台かありますけれども、 頻繁な段取り換えに対応できない、新規受注品は準備している間がないといった事で、 ローダーを使うのは今や1品目2工程だけになってしまいました. 熱変位は油温コントローラでかなり抑えられますし、 工具磨耗による寸法の変動に対しては、傾向を掴んでしまえば、 カウンター掛けて品確したり、マクロ等プログラムで一定の補正を入れる事も可能ですが、 極小ロットですと、変動状況を把握できる前に仕事が終わってしまいます. チャッキングのバラつきなどは、着座検知等の併用である程度抑えられますが、 構造や手順をよく考えないと人間がやる以上に時間を費やしてしまう事にもなります. 普通に考えれば数十個のロットでローディングを自動化する利点というのはあまり無い訳ですが、 例えば、同径・長さ違いのワークの加工が連続したりすればそれなりに効果が上がる可能性はあります. こういったアプローチは機械のNC化が進む前から専用機では日常茶飯事ですが、 専用性が高いために装置が個別製作になり易く、 パンフレット等には共通項目など基本的な事項しか書けないという事もあります. 自動機系NC旋盤はミヤノとかツガミとか、あとは村田機械とか、 半専用機系NC旋盤はアマダグループの旧テクノワシノあたりが得意としているかな. 今では森やオークマなど汎用機系のメーカーも自動化装置は手掛けていますが、 自動機・専用機系のメーカーというのは、長くやっているだけあって、 それぞれ「ならでは」なものを持っていたりします. また、後付けローディング装置のメーカーというのもあります.
その他の回答 (3)
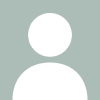
前出の回答者の皆様が紳士的かつ適切な回答をされておられます。 私なら「だめ!だめ! そんなのメリットよりデメリットの方が多いよ!」 と言ってしまいそう。 理由として 通常NC旋盤のチャックは油圧の3爪でメーカーの保証値は繰返し精度0.02程度 爪のセルフカットが下手ならもっと悪い (これはコレットチャックなど対応出来る) ワークの長さと外形の関係でストッカーの選定やローダーの選定が大きく変わる。 多分、貴殿も上司の方もローダーの段取り工程を見られた事が無いと想像します。 1個のワークで表裏2回の段取りが必要 加工は作業者の頭の中で加工が出来て段取りが終ればば70%は仕事が出来ている 後の30%で実切削 1個の加工なら汎用機の方が早い事が多いのも事実 加工個数が少なければ効果はありません。 作業効率を上げたいなら段取り時間の削減方法を考える ワークの加工中でもプログラムを作成できるようにするとか 対話型の採用 タッチセッター等の採用で段取りを簡易化 油圧チャックを汎用のスクロールチャックに交換 汎用機型 簡易NC旋盤の導入 などの方法が良いのでは? ついでに (一般公差±0.01程度)とされておられるが 確かに±0.01の精度要求は多くなっています。 JIS B 0405・B 0419 では f(精級)で0.5以上3以下の公差は±0.05 30を越え120以下の公差で±0.15の許容差です。 一般要求以上の精度と認識しておいた方がトラブルは少ないと思います。
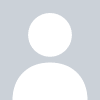
お礼
おっしゃることはごもっともと思います。 実際に何社か電話させてもらった自動化EG会社では、 「だめ!だめ! そんなのメリットよりデメリットの方が多いよ!」 というようなことを言われました。 ただ、作業の効率化ともなるとさらに果てしない道のりになってしまうので 自動化に一区切りついた後に、ひとまずは保留しておこうと思います。 回答ありがとうございます。
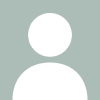
質問者さんのような多品種小ロット部品加工を自動化するために、 自動チャック爪交換+ワーク搬送用のガントリーローダを付けた 対向2スピンドルのスペシャルCNC旋盤を導入した事例を知って いますが、機械の運用(スケジューリング,プログラム作成とチェック, 刃具の管理,機械のメンテ)が大変で、成功したとは言い難い...との 感想です。 オークマさん、森精機さん、中村留精密さんなどのCNC旋盤に強い メーカであれば、経験に基づいた最適なシステムをトータルパッケージ として提案してもらえるのですが...。 後付となると、参考URLのメーカさんは如何でしょうか。 (既に相談されていたら申し訳ございません) また、回答(1)さんのおっしゃられるとおり、段取りの手間や加工精度 の問題が極めて重要です。現在、時間が掛かっている作業の効率化を テーマとして、「自動化」はその一手段と捉えて、ご検討することを お奨めいたします。
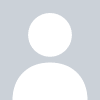
お礼
回答ありがとうございます。 導入のうまくいかなかった例はメーカーなどになかなか聞くことができず非常にためになります。 ガントリー式のオートローダーは1000万単位でコストがかかってしまうので、このご時世にはなかなか導入は難しいですね。 シリンダー式のものも、製品が絞られたり通常の加工がしづらくなったりとなかなかに難しそうです。
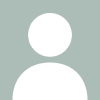
弊社でもローダー使用を使って旋盤加工しています。 御社と違い量産物です。 20個以下のロットとなると段取り回数が多くなる為 治工具の共用化、ワークストッカー、払い出しストッカー等の 部品を簡単に交換する方法などを考えないと段取りにすごく時間を 費やしてしまうことになります。 また、公差も厳しい為自動計測を導入しないとならず 費用もかかりそうですね。 また、チョコ停、圧痕の問題もあります。 いずれにしてもどちらが徳かを考えなければならないでしょう。 ローダーを設置した場合、段取りが終わり無人加工出来る時間が どの位あるのかをシュミレーションしたほうがいいでしょう。 段取りに3時間かけ無人加工が30分だけではせっかく自動化しても 省人とはなりませんし。
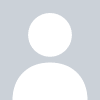
お礼
早速の回答ありがとうございます。参考にさせていただきます。 自動化の資料や知識を集めるにつれて、乗り越える壁がどんどん高くなるのを感じますが、めげずにがんばります。
お礼
細部まで行き届いた回答をありがとうございます。 私は直接、NC旋盤の加工者ではないので加工者目線のご意見はありがたいです。 (弊社のNC旋盤の加工者に聞けばよいのですが、現状が人手による加工なので自動化の機能や各種方法について理解してもらって、メリットを説明したうえで可否を聞くのはなかなか難しい面もあります。) 大変参考になりました。 このようなあいまいな質問に答えてくださって、ありがとうございます。 皆様に良回答を差し上げたいのですが、そういうわけにもいかないので二つ選ばせていただいて回答を締め切ります。 この欄をかりて再度回答者の皆様にお礼申し上げます。 ありがとうございました。